Applications
Take products above and beyond with Origami Composites
Our technology unlocks advanced functionality from common materials by leveraging the concepts of origami to impart structure, flex, and enhanced mechanical properties.
Below are some examples of advanced functionalities achieved with Origami Composites.
Lightweighting +
Lightweight materials exist in may forms, from fiber-reinforced composites and foams to lattices and honeycombs.
Origami Composites go further, using commodity materials to create exceptional shear strength – something foams and honeycomb can’t touch.
Our flagship product, ArmorONE sandwich panels incorporate an Origami Composite MetaCORE® that’s ideal for affordable strength and lightweighting – like the wall paneling used in dry van trailers, straight trucks, box trucks, and cargo vans, as well as roll-up and swing doors, garage doors, and wall partitions.
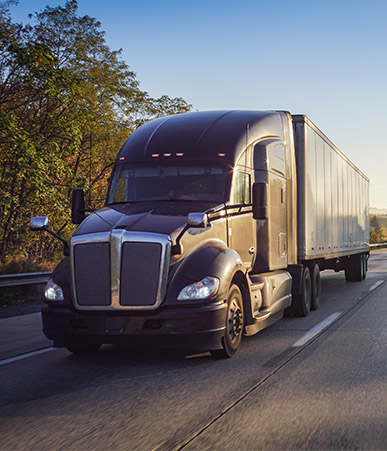
Flexibility
Origami Composites can be used to overcome extreme thermal and mechanical stresses by expanding and flexing while maintaining form and structural integrity.
One application of this is Enhanced Geothermal System components. Where harsh, hot conditions deep underground cause flexible rubber-like materials to fail, Origami Composites endure. Origami Composite O-rings are made from a more robust material imparted with geometric design. The design allows for flex and expansion, without corrosion or degradation of the underlying material when exposed to extreme downhole conditions and temperatures.
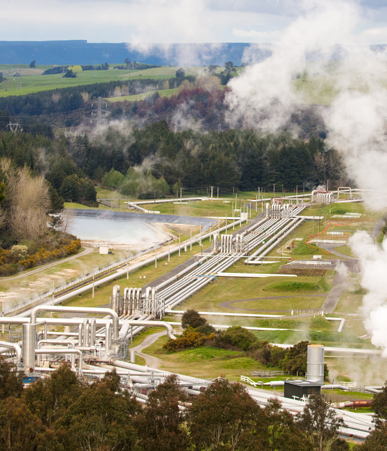
Insulation and thermal management
Traditional insulating materials like foams and wools are used in all manner of applications, from building materials to premium coolers. Compared to advanced products like aerogels and vacuum insulated panels (VIPs), they are cheap – but the trade-off is low performance. Aerogels and VIPs may perform better, but they are fragile and costly.
Origami Composites, on the other hand, can be designed with high R-values while being cost effective. They offer substantially better shear strength – the result of being rationally designed rather than randomly formed. Foams fail primarily via shear, so origami composites offer a considerably increased material life span.
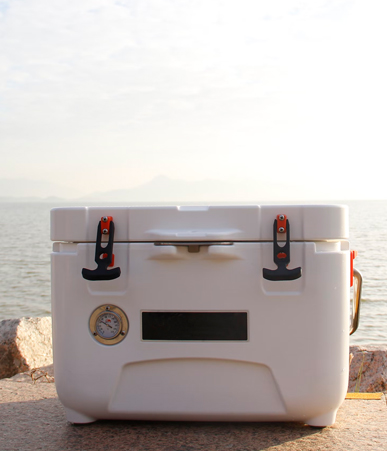
Auxetic properties
Normal materials are meiotic, meaning they shrink when pulled and grow when pushed – think modeling clay or a seat cushion. Origami Composites can be designed with mechanical properties that normal materials can’t possess, like being auxetic – growing when pulled and shrinking when pushed.
By physically or mechanically compressing an auxetic Origami Composite into a space, it will shrink. When the pressure is relieved, it will expand to fill the available space and press against the cavity.
The ability to “press-fit” offers benefits to a range of industries, including building construction, where installation of spray foam is unreliable and suffers long-term compressive strength degradation.
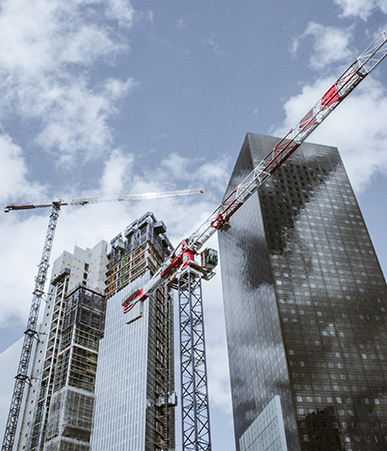
Acoustic control
Starting as a flat sheet that has curves or creases built into it, Origami Composites take on a three dimensional shape. This shape can be designed to conform to architectural surfaces, as well as having a texture that promotes acoustic damping or sharpens the sound to meet at a single point – like a whispering gallery or the design of a concert hall.
There is no qualitatively different manufacturing method required to do this kind of shape optimization, only mathematical design that maps the initial flat materials into a final 3D shape, giving Origami Composites the edge in acoustic engineering.
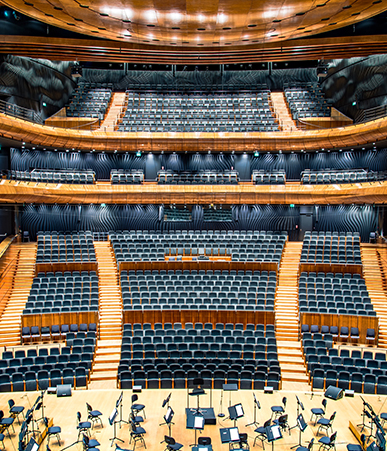
Part consolidation
By the nature of their design, Origami Composites can be used to consolidate system parts, allowing two or more objectives to be performed simultaneously.
A great example of a system that would benefit from part consolidation is electric vehicle battery boxes, where the batteries must be held safely without overheating. Current battery boxes consist of many parts to accomplish this requirement, including an aluminum crash structure and a cooling system – taking up space and time to assemble. An Origami Composite structure could reduce the amount of assembly required, potentially lower the weight, and provide crash protection to the battery while cooling it – all within a single layer.
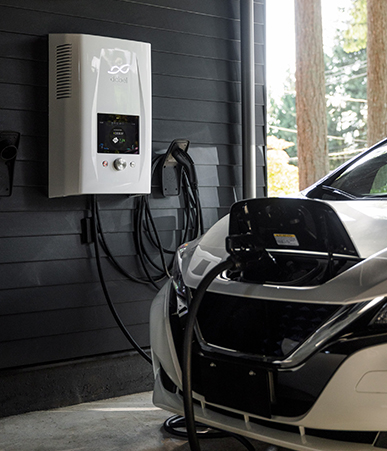
Contact us today to discuss purchase or licensing options
1-866-778-6415 | sales@armorytechnologies.com